Ossid Automates the Weigh Price Labeling Processes for California Cheese Manufacturer
With a booming economy and the dawn of the Roaring 1920’s culture renaissance, it was an exciting time for Americans following the end of World War I. And for the three Rumiano brothers of Fred, John, and Richard, it meant the launch of their cheese business.
These trio emigrated from Italy at the turn of the century. After working in gold mines, shipyards, and liquor plants, they capitalized on the growing presence of cheeses in America by starting Rumiano Bros in the early 1920s with distribution around San Francisco.
More than 100 years have passed, and Willows, California-based Rumiano Cheese (https://rumianocheese.com/) has stood the test of time. The company is still owned by the Rumiano family, with fourth-generation sons Joby, Tony, and Ray Rumiano overseeing the full-service processing operation. Today, the company’s products are sold online, as well as retail outlets in all 50 states.
A lot can change over 100 years. As Rumiano Cheese continues to grow, so does the technology available to help package and label its products.
A Better Whey
One area of its packaging operations Rumiano Cheese was looking to upgrade was its labeling system. Labeling cheese can be particularly challenging because of its various weights, shapes, and sizes, meaning pricing varies from unit to unit. Since its founding, Rumiano products have been labeled by hand, a time-consuming, inefficient process that took several employees to oversee.
“I had been labelling cheese by hand since I was 15 years old. Every piece of cheese was touched by somebody multiple times. This method was not efficient enough for our required throughput, and it also ran the risk of injury to our employees from repetitive motion,” Ray Rumiano said.
In order to boost speed and add efficiency to their packaging lines, Rumiano Cheese turned to the NextGen 2115 Weigh Price Labelers (WPL) from Ossid (www.ossid.com), a North Carolina-based food packaging OEM of weigh price labeling systems, as well as tray overwrapping, thermoforming, vacuum skin, and other packaging solutions. Ossid is part of ProMach, a company of 47 product brands that operate across the entire packaging spectrum.
The 2115 NextGen WPLs provided an immediate boost to efficiency by weighing, calculating price, and labeling 60-80 pieces per minute with multiple label heads on the top and bottom of packaged cheese. This automated system provides the additional benefit of consistency, with each label placed on the product in the same position at the same angle with more reliability than human workers can achieve. Shoppers can look through an entire shelf of products packaged at Rumiano Cheese and see perfect alignment for a polished, eye-catching look.
From Good to Grate
While the machine’s capabilities made a huge and immediate impact on production, the customer-oriented design is what sets Ossid apart.
“We worked closely with Rumiano Cheese throughout the design process,” said Jared Rangle, Sales Representative, Ossid. “The belt on the machine is at the right height for employees to load without putting stress on their back, and the materials in the unit are sanitary for easy cleaning.”
Changeovers are fast and easy. All the company’s labeling information for each product is preloaded into the machine, meaning employees simply select the correct labeling recipe for the product being run, and the 2115 NextGen WPL handles the rest.
The NextGen 2115 Weigh Price Labeler features an all-new control system that combines machine controls and system software into one processing unit for faster weighing, processing, and labeling times. The machine incorporates the latest National Type Evaluation Program (NTEP) approved load cell and measurement electronic technology.
All About the Cheddar
Like most businesses, one of the biggest stressors for Rumiano Cheese is maintaining a strong bottom line. The 2115 NextGen WPLs assist in this area by allowing staff to handle other areas of operation where their skills can be put to better use. For example, those operators on the line become more skilled employees through training to run other newer automation systems. They become more valuable to their organization, and their earning power increases – it’s really a win-win situation for all involved.
“Implementing equipment like this has been a game changer for employee retention,” Ray Rumiano said. “People realize that this is a state-of-the-art place to work where they can learn about new equipment and gain new skills. It makes them want to stay.”
Rumiano Cheese operates two 2115 NextGen WPLs, both of which were installed in January of 2023.
Increasing output without increasing cost has also allowed the company to focus on continuing their ancestors’ legacy. Its new plant in Willows, California, realized a 40-plus year dream for Baird and John Rumiano to double its packaging volume by 2025.
“Our entire business is highly committed to ethical animal treatment and care for the environment,” Ray Rumiano says. “We have our own flagship brand, Rumiano Organic, which only sources dairy from free pasture cows; we partner with more than 20 different family-owned dairies in the Humboldt and Del Norte counties of California’s northern Redwood coast. Additionally, a key part to our overall success is the relationships we have with packaging OEMs like Ossid.
“The cost savings we have seen from working with Ossid have allowed us to remain competitive, become more efficient, and meet our production goals. We are excited for what is to come and will turn to Ossid for any future WPL needs.”
Ossid Automates the Weigh Price Labeling Processes for California Cheese Manufacturer
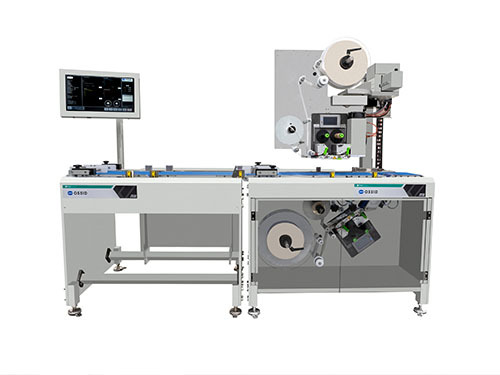